Sustainable Transformation Makes Any Business More Robust
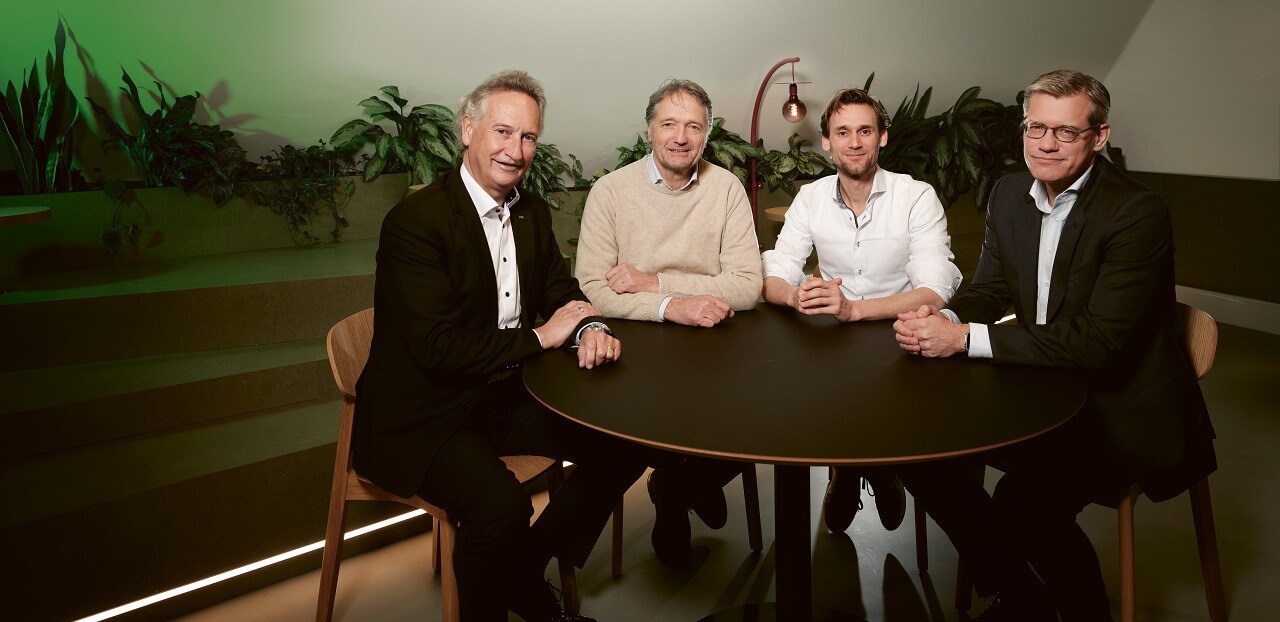
06-02-2024 | Interviewer: Remko de Bruijn | Author: Emely Nobis | Image: Rogier Veldman
Even though the participants at this roundtable on sustainable product development are each pioneering in their own sector, they have never met before. Even before the discussion, led by Remko de Bruijn of consultancy firm Kearney, officially begins, they enquire about each other’s business models and there is a lot of mutual recognition - despite major differences in the size and growth stage of their companies. Startup Maeve Aerospace, founded in 2021, designs hybrid aircraft that can cover distances up to 1,482 kilometers, consume 40 percent less fuel in the process and will also refuel only with e-fuels. The first plane, however, has yet to be built. Founder and CEO Jan Willem Heinen: ‘The first flight will be in 2029 and entry into service is planned for 2031.’
Medium-sized MUD Jeans, which makes and recycles sustainable jeans, was founded in 2012 by Bert van Son. Before that, he worked in the clothing industry for 25 years. ‘I saw that degenerate from a wonderful industry where people were paid well and could work cleanly, to an industry where everything has to be made as cheaply as possible without thinking about how, by whom and with what waste materials. I wanted to change that by making the biggest product - jeans - more sustainable.’
The biggest ‘player’ at the table is Executive Director Maurice Geraets of global company NXP Semiconductors Netherlands, which emerged almost 18 years ago from Philips’ former semiconductor division. The 50 to 60 billion chips the company produces annually are in cars, antennas for mobile networks and smartphones for contactless payments, among other things. ‘We invest 17 percent of our revenues in research and development, including making chips more energy efficient. 100 tons of CO2 reduction in our industry leads to a reduction of 500 tons in the rest of the world, because those chips enable solar panels, windmills, electrification of cars or electric flying. That means our impact can be huge. In 2020, we were one of the first companies to issue green bonds. With that, we then raised a billion dollars to invest in innovations for sustainability.’
Sustainability is not only about developing products that last longer, reduce emissions or are energy efficient, for example, but also about what happens end of life. For example, most depreciated aircraft end up in a graveyard in the Arizona desert. Where in the life cycle is the biggest impact of your business model?
Van Son: ‘With us, recycling is in the business model from the very beginning. That is precisely what makes it complicated. Making jeans sustainable is not that difficult at all. If consumers are willing to pay for it, you can make every step in the production process, from cotton and yarn to dyeing and transportation, better. Recycling, on the other hand, is very complex in the garment industry, almost impossible, because so many different materials are used.
That is why we created a monostream from one material: cotton. Our own pants, for which we set up a leasing system, consist almost exclusively of cotton. The technology to make excellent new yarns from that is getting better and better. That is why we now also take in pants from other producers, pants that consist of at least 95 percent cotton. Currently, a maximum of 40 percent of our raw material comes from recycled material, but the dot on the horizon is 100 percent new jeans made from old jeans. Ultimately, the people of Amsterdam must become our cotton supplier, so to speak.’
Heinen: ‘Frankly, we are not in the business of recycling. An airplane is in the air for 20 years seven days a week and 350 days a year. The real emissions come from the engines, so that is where our focus and our right to exist lies. Airlines do not like new suppliers, because the risk that something goes wrong is huge: from financing to certification. You have to have a very good reason to be able to sell an aircraft as a newcomer. Our right to exist is emission reduction; we take our responsibility in that. That is also why we guarantee that whoever buys our aircraft has access to 100 percent sustainable fuel. To achieve that, we are creating partnerships with other companies.’
NXP wants to advance the sustainability transition by working on more energy-efficient chips. Is recycling - also given the shortage of critical metals - also on the agenda?
Geraets: ‘In one chip of usually much less than a square centimeter, there are as many as 100 different materials. Unraveling them is not yet possible. Research is being done, but for the time being I do not see any industrial application. We therefore focus on innovations with the greatest impact. Besides more energy-efficient chips, there are mainly two routes. The first is to reduce electronics in a product, for example, by solving what you put in a chip now by software. In our latest NFC chip for contactless payments, we have integrated an eSIM, a SIM card that is not physical but software on our chip. By doing this, you not only extend the life of a product by making it software upgradable: if you no longer need a physical SIM card, you do not have to replace or recycle it.
The second route to positive impact is to replace poor materials from a sustainability point of view with environmentally less harmful raw materials. This is where we make a major contribution. If you use gold to position a chip, the CO2 impact of the mining is thousands of times greater than with copper, even if you were to recycle the gold. So, it is better to use copper, but because copper has different properties than gold, we first needed considerable research to be able to make that move. We have now successfully made the switch from gold to copper.’
What are the biggest challenges when it comes to achieving your sustainability ambitions?
Geraets: ‘For us, that is geopolitics. We spent the last 30 years setting up our chain with maximum efficiency with very limited government involvement. That is changing. If America wants to use only chips produced in America, that is not necessarily as efficient or even more sustainable than if they are produced in Taiwan. Chips take up so little space that transportation is a very small part of the climate impact percentage-wise - although you have to work to improve that too.
Geopolitics also plays a role in the enormous dependence on China, where many critical raw materials come from. An average car contains 1,000 chips. If even a few are lacking, that car often cannot roll off the assembly line. We have to think about reducing geographical risks.’
Heinen: ‘We discovered that it is very difficult to make an industry sustainable that is not yet ready to do so. We were founded with the goal of developing an all-electric passenger aircraft. To make that happen, we raised several million and put a team on it that developed a model for up to 44 passengers and a range of up to 460 kilometers. Ideal for short distances, we thought in our naiveté. When we presented our prototype at the Air Show in Paris in early 2023, the message from the airlines was clear. They did not want it, partly because Schiphol and similar airports are enormously busy and with larger planes you have fewer flight movements and a longer range. That rejection was really a blow to us. Eventually we came to the conclusion that building an all-electric aircraft is too big a risk and we started working on a hybrid model with e-fuels. And then Europe is still in the lead when it comes to sustainability. In Asia or India, cost per seat is the only consideration. This is another reason why the choice for hybrid is better, because then the cost per seat is acceptable and you have a sustainable impact.’
Van Son: ‘The fashion industry is also not really ready for sustainability. A lot of people make a lot of money by doing business in a fairly irresponsible way. We make jeans with a good price-quality ratio, a beautiful washing, a great fit and which are also sustainable. But sustainability, according to our own research, only ranks 14th in considerations when buying jeans. I struggle with the question of how to convince people that it is better to buy a good pair of jeans that will last them longer once a year than to buy one that is not made very responsibly and with which they are wearing poison on their skin thanks to the use of chemicals, four times a year. That probably only works with far more brand awareness, but as a small player it is almost impossible to compete with the marketing machines of big brands like Levi’s or G-Star. Besides online, we sell our pants in about 300 stores in Europe. But at Bijenkorf, for example, we were out of business after three seasons because people still choose the familiar names. That is extremely unfortunate, and we have to come up with something to address this.’
How important is collaboration with customers to achieve your sustainability goals?
Geraets: ‘The customer is key. Last September Tim Cook of Apple was a guest at our headquarters in Eindhoven to emphasize that we are helping them to become more sustainable. Conversely, if we do not integrate our eSIM with the NFC chip for contactless payment, that innovation will not reach the market. The technology for eSIM is at least 20 years old, but for a long time the telecom companies did not want it because it makes it easier for consumers to switch providers. That too shows how important it is for the customer to embrace your product.’
Being successful as a forerunner in innovation, of course, ultimately requires scale. What helps to get scale?
Van Son: ‘Cooperation with other companies is one possibility. For example, some time ago IKEA asked us to make a sustainable denim cover for a bench. Suddenly we could go to our supplier and say we wanted to buy 100,000 meters of cotton. You can then access better quality, a better price and fast delivery ... that is a huge swing.’
Geraets: ‘A few years after we left Philips, we developed a strategy in which we focused only on segments in which we are the largest worldwide and half the size bigger than number two. Otherwise, we are not going to do it. When you go through the gate at a ski elevator with your pass, there is a 70 percent chance that our chip is in it - because we have a huge market share on that. The same goes for the chip in your car radio or in Apple Pay on your smartphone. We can only be effective with scale. After all, developing a chip costs millions, while the customer may pay less than a dollar or sometimes even less than a penny for it.’
Heinen: ‘Economies of scale will only come into view for us if we succeed in producing non-fossil hydrocarbons and making e-fuels from them. If aviation starts using these en masse, we will have solved the climate problem. I am hopeful about that. The aviation industry is so visible, I guess it will eventually be forced to pay to develop e-fuels.’
As forerunners in sustainability, what would you like to pass on to corporate Netherlands?
Heinen: ‘I would definitely like to change scope 3 (indirect emissions of CO2, caused by another organization’s business activities, ed.) from something you do not want to do to a major competitive advantage. The fossil industry still seems little motivated to start working with non-fossil hydrocarbons. I do not understand that. An oil or gas company that is already exploring how to extract hydrocarbons from the air has a niche to grab, will get better and better at it, and will be among the winners in 10 to 20 years.’
Geraets: ‘I think executives will ultimately be more successful if they accelerate the transitions we are all facing - digitalization, sustainability, electrification, artificial intelligence - in their businesses. It will only make it more robust. Our factory in Nijmegen runs 24/7 and, with 700 people, delivers an enormous output that is also cost-efficient, sustainable and of good quality. Without effort in all those areas, it would never have been possible.’
Van Son: ‘When I recently attended the Supervisory Board Cycle at Nyenrode, I was shocked at the limited extent to which sustainability still is on the agenda. My appeal to directors and supervisory directors is to inform themselves well, seriously investigate where their company is not doing well, express this out loud and then just get on with it.’
This article was published in Management Scope 02 2024.
This article was last changed on 06-02-2024